Steel Structures for Industrialized Houses and Homes
The enormous versatility, reliability and resistance of our system has led us to be able to offer metal structures for homes built with our patented system. To this end, we have developed and incorporated into our parts and systems the best materials and solutions on the market for building… This results in buildings that are highly resistant and energy efficient (A-rated in all areas), as well as modern, very comfortable and beautiful.
In this article, we will explore the benefits of building steel framed homes, showcase examples of steel framed homes, and highlight the versatile systems offered by StarModul Steel Framing 2.0. Join us to discover the world of metal structures for houses.
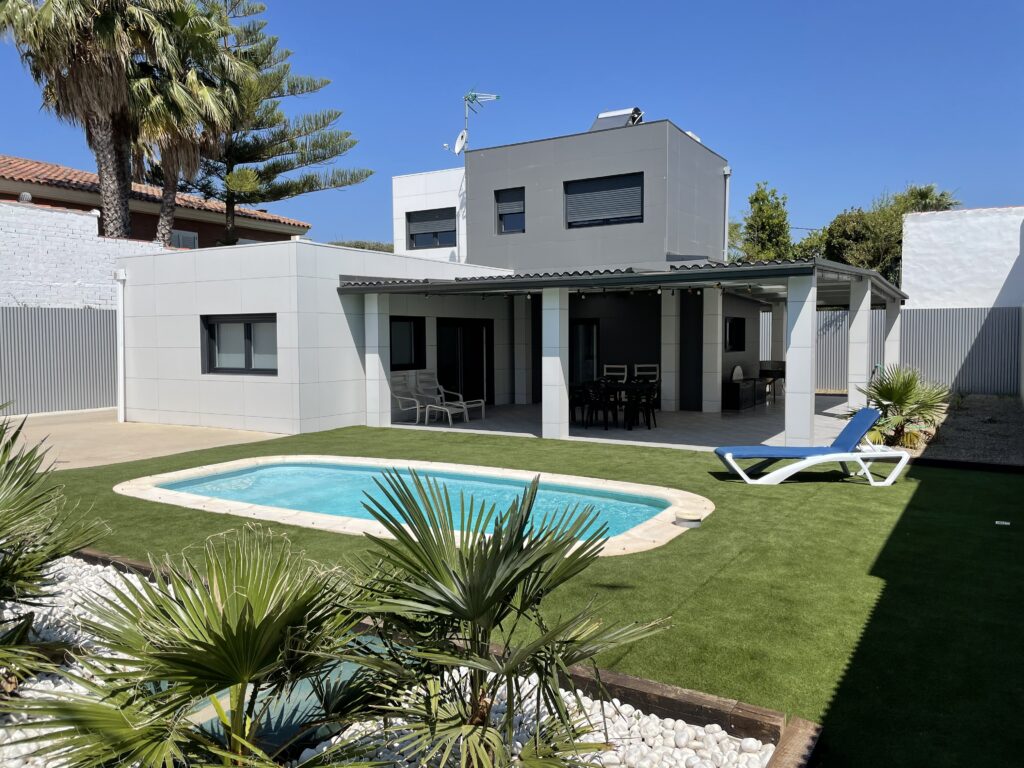
StarModul Industrialized Houses - Construction Details
No other system on the market comes close to Starmodul’s innovative solution for prefabricated and modular steel houses. With its patented joining system, more than 100 different parts and customer support throughout the design process, Starmodul offers a cost-effective, efficient and flexible option for the construction of metal structures. Read on to discover more about the benefits and details of Starmodul’s system for building strong and versatile homes.
If you’re considering modular construction for your next project, Starmodul is the name you can trust. With its experience, commitment and innovative solutions, Starmodul simplifies the construction process and delivers outstanding results.
Contact Starmodul today and explore the possibilities of modular construction for your next home.
FOUNDATION
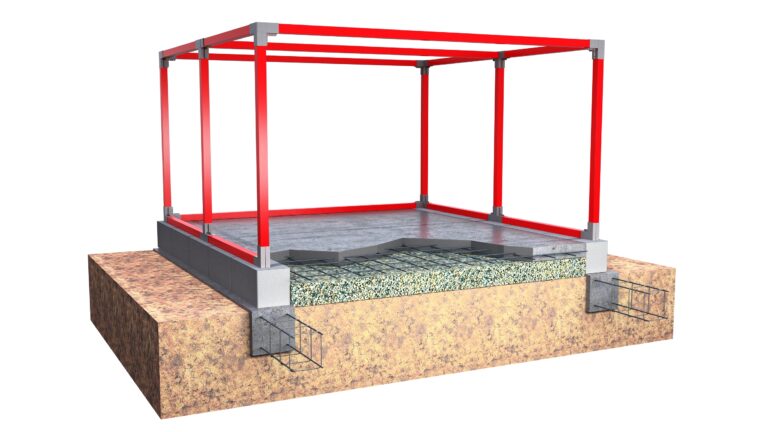
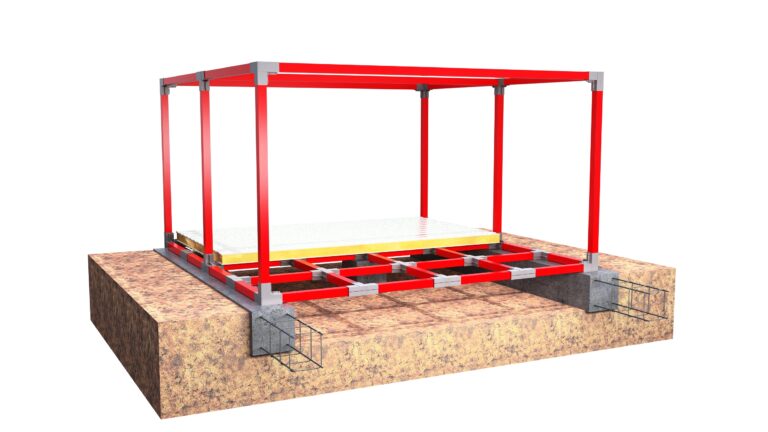
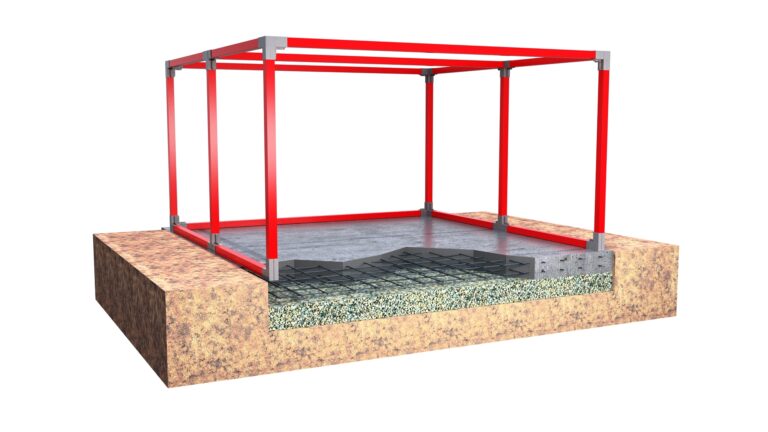
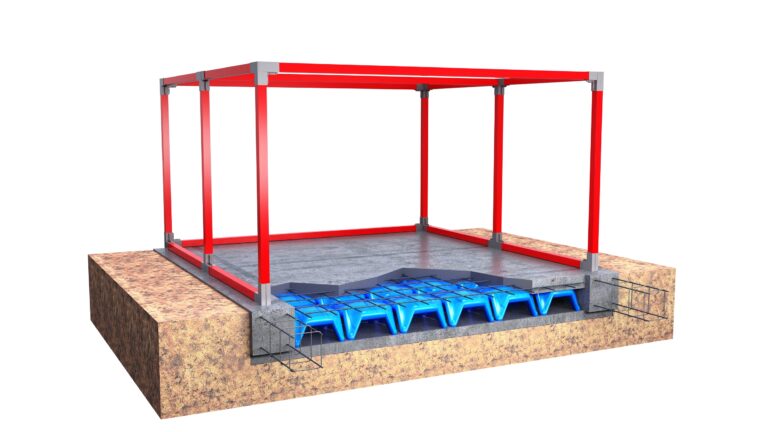
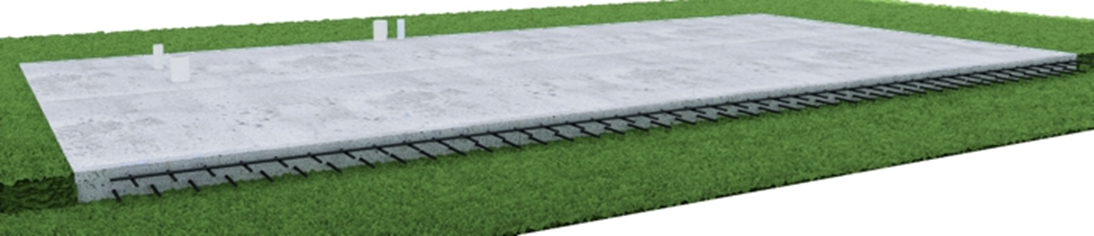
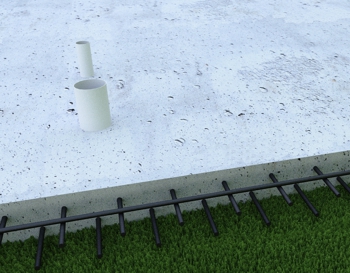
Our buildings, among their many advantages, have the characteristic of being self-supporting and lightweight.
These two characteristics mean that the foundation requirements are minimal, since they do not exceed a load of more than a few hundred grams per square centimeter.
The reinforced concrete slab is the ideal solution, because it is possible, at the same time as building it, to insulate it thermally, to make it the sanitary slab, to act as a substrate for the various conduits and the base for the flooring, heating, etc.
Other solutions are also accepted, such as continuous beam foundations, braced shafts, pile foundations, etc.
In the example on the left, we can see what would be a suitable slab foundation solution, while at the same time complying with the requirements of the CTE.
Reinforced concrete slab
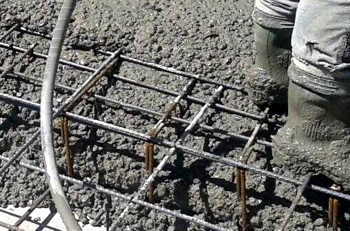
Manufacture in concrete plant (HA-30/B/20/IIb) and pouring on site.
Reinforced with EM 15X20 electro-welded mesh, diameter 8 mm, and 10 mm reinforcements.
Steel type B 500 T 6X2,20 UNE 36092.
Expansion joints grouted with cement grout 1/3 CEM II/A-P 32.5 R and cleaning, according to NTE-RSR.
STRUCTURE
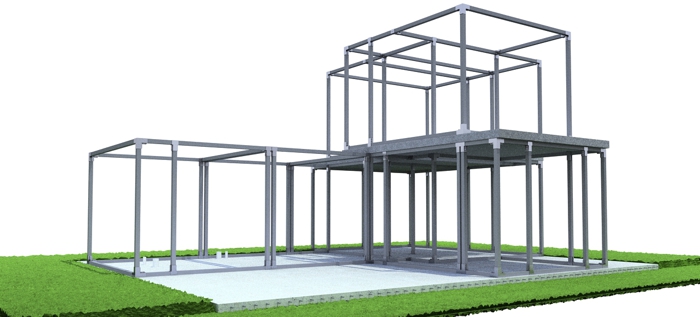
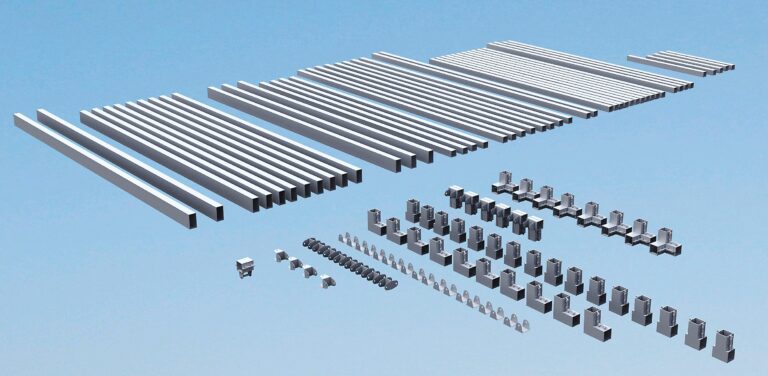
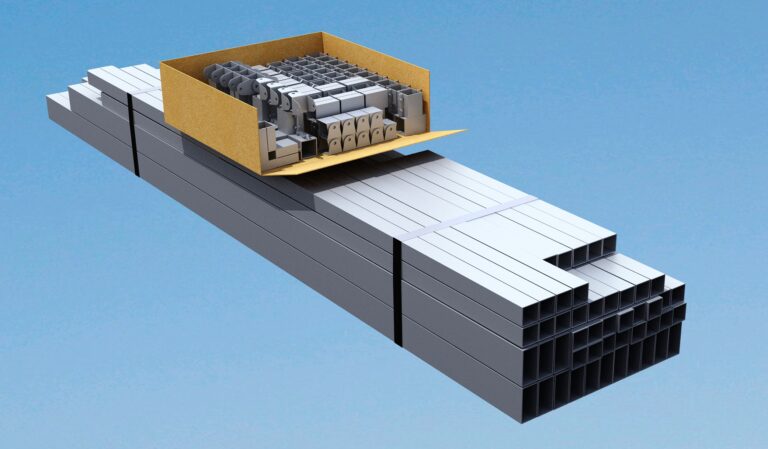
The assembly of the structure is carried out on the slab, set and leveled (although the system allows for substantial variations in this regard).
After the staking out, the different pieces and assemblies that make up the structure are formed; porticoes, brace braces… However, in an extremely simple way, assembling the pieces and screwing them into the knots, without the need for brackets or other adjustment elements, since the knots themselves “drive” the bars to the appropriate angles.
The fixing of the structure to the foundation slab is carried out in two phases:
In the first one we anchor it by means of special pieces (see details of pieces, below), which fix a mechanical grip by means of special high-strength bolts.
In a second phase, we embed part of the nodes, supports and steel braces in a high-strength mortar, which will serve as the base of the pavements (see points 04 and 10).
The resources necessary for the assembly of the structure are reduced to a minimum for several reasons.
L he weights that are handled are very low because we always work with light individual elements.
The assembly is self-driven in terms of the angular positions of the parts, and it is not necessary to cut at an angle or “square”.
A ratchet, open-end wrench, drill and riveter (and not always) are all we need to assemble it.
CLOSINGS
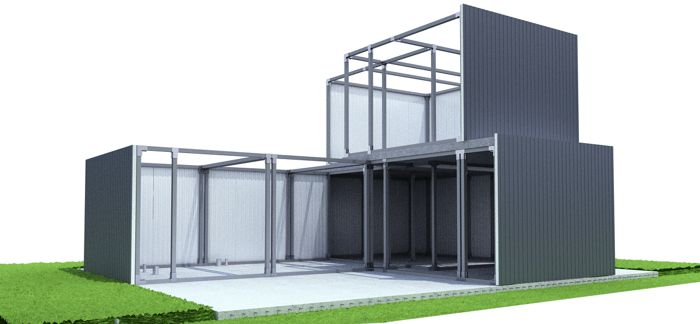
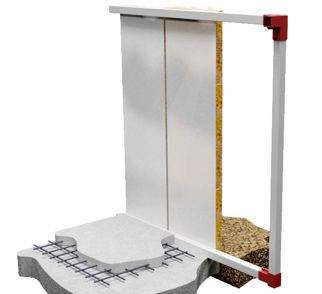
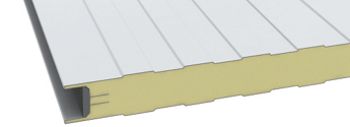
The
enclosures
are made of steel Sandwich Panel, with polyurethane filling, of the type used for cold rooms.
This panel has a high mechanical resistance and full guarantees of watertightness on any structure, in addition to the highest specifications in thermal insulation.
The thickness is 100 mm, which gives the building a spectacular insulation coefficient.
The useful width of these panels is 1 m, tongue and groove and perfectly sealed between them and the structure.
Its high solidity collaborates with the structure, giving the building a self-supporting character of very high resistance, insulation and durability, as well as a practically inexistent maintenance.
0.4mm steel plate | Inner Face | 0.4mm steel plate |
---|---|
Isolation | Polyurethane expa. of 40Kg/m3 |
Thickness | 100mm |
Outer Face | 0.4mm steel plate |
Type Plate | Lacquered of 5 microns |
Resistance
to the fire
| CS3DO |
Fixing | Hardware mechanics |
Thermal conductivity | 22mW/mK |
Range of application | -40º to +80º. |
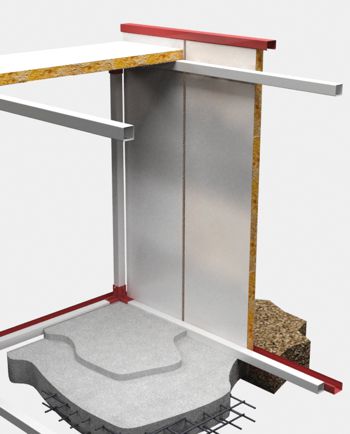
The
ease of assembly
of these enclosures is due to the fact that we have applied in their design all our experience in this field, which goes back several decades, and to which we have been incorporating those of third parties.
Everything has been foreseen; every detail has been worked out in advance and all the necessary accessories have been designed and manufactured for a quick and perfect assembly.
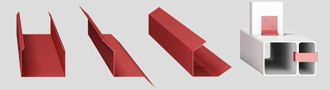
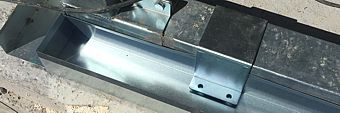
COVERS
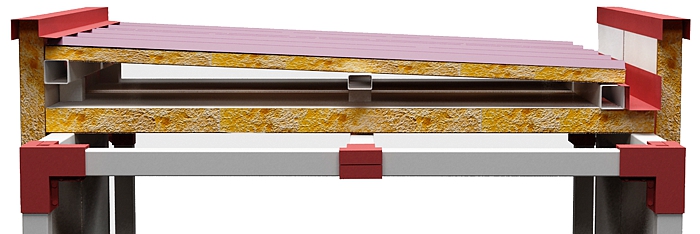
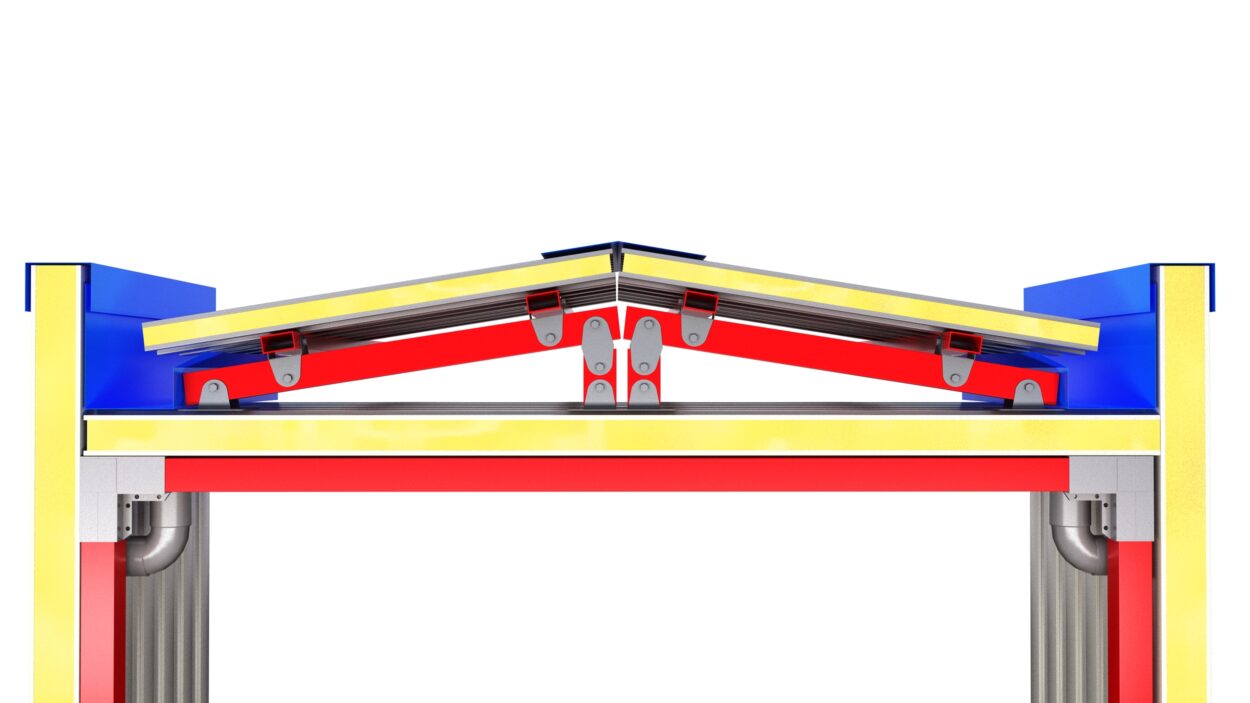
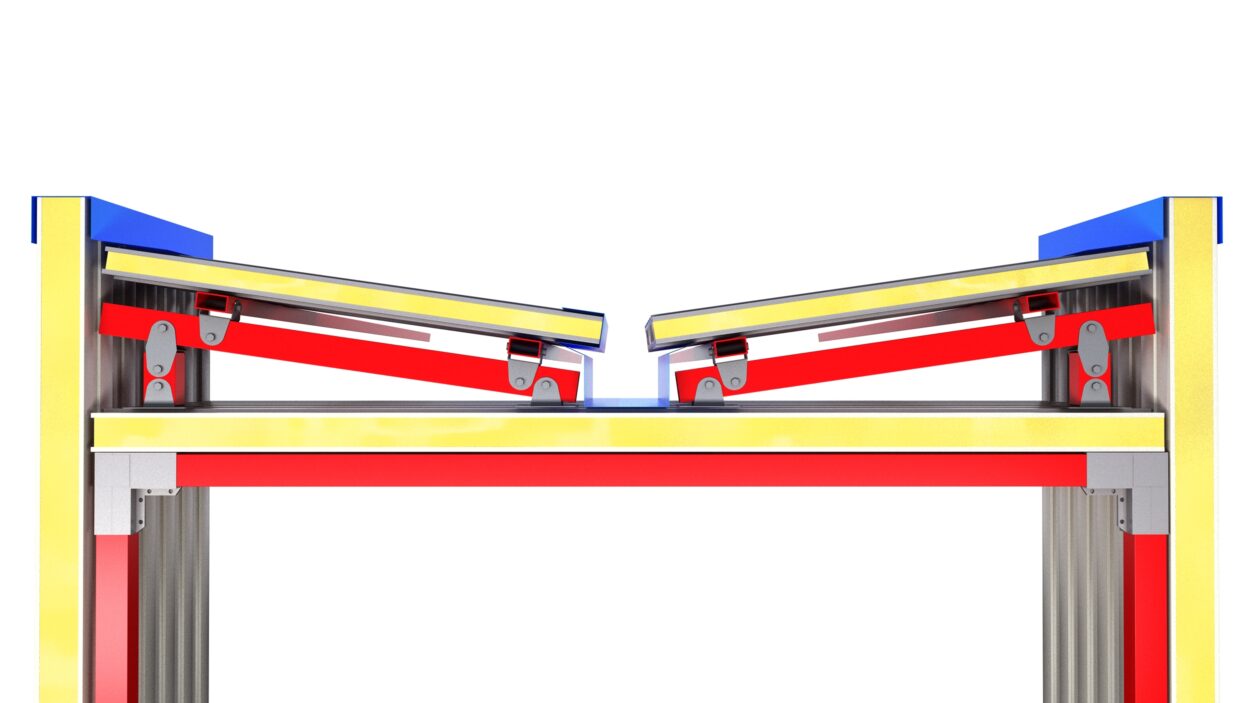
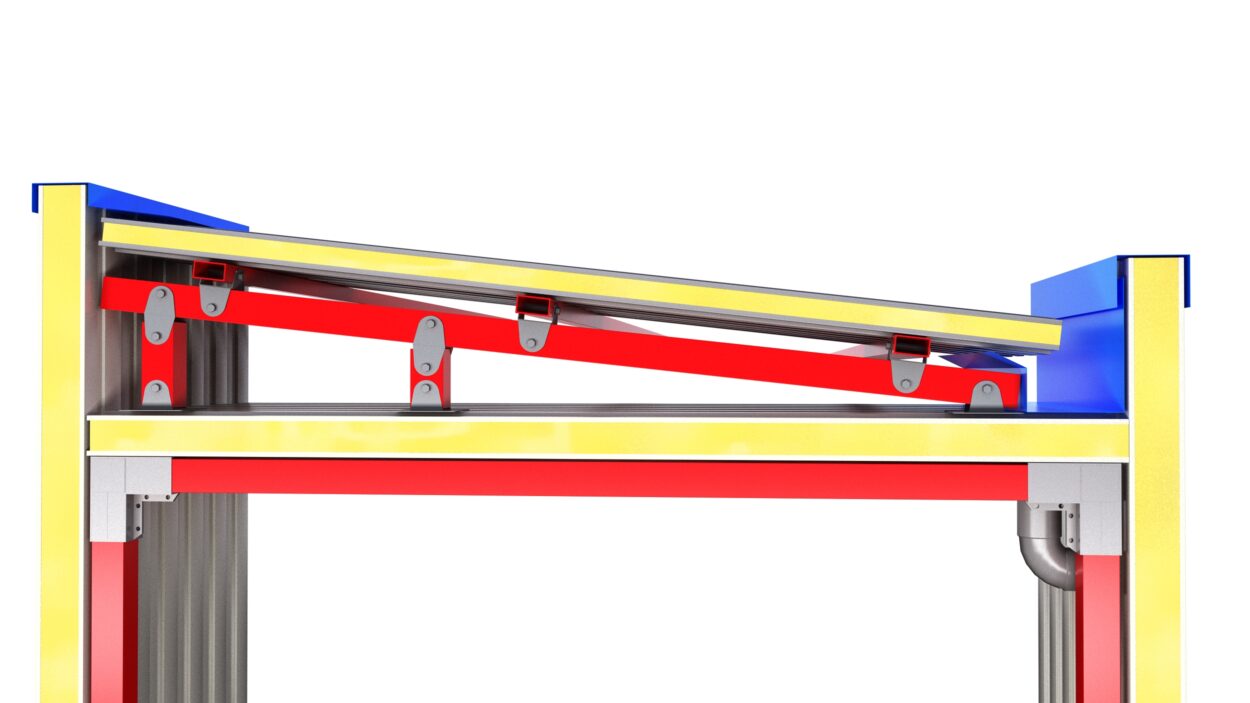
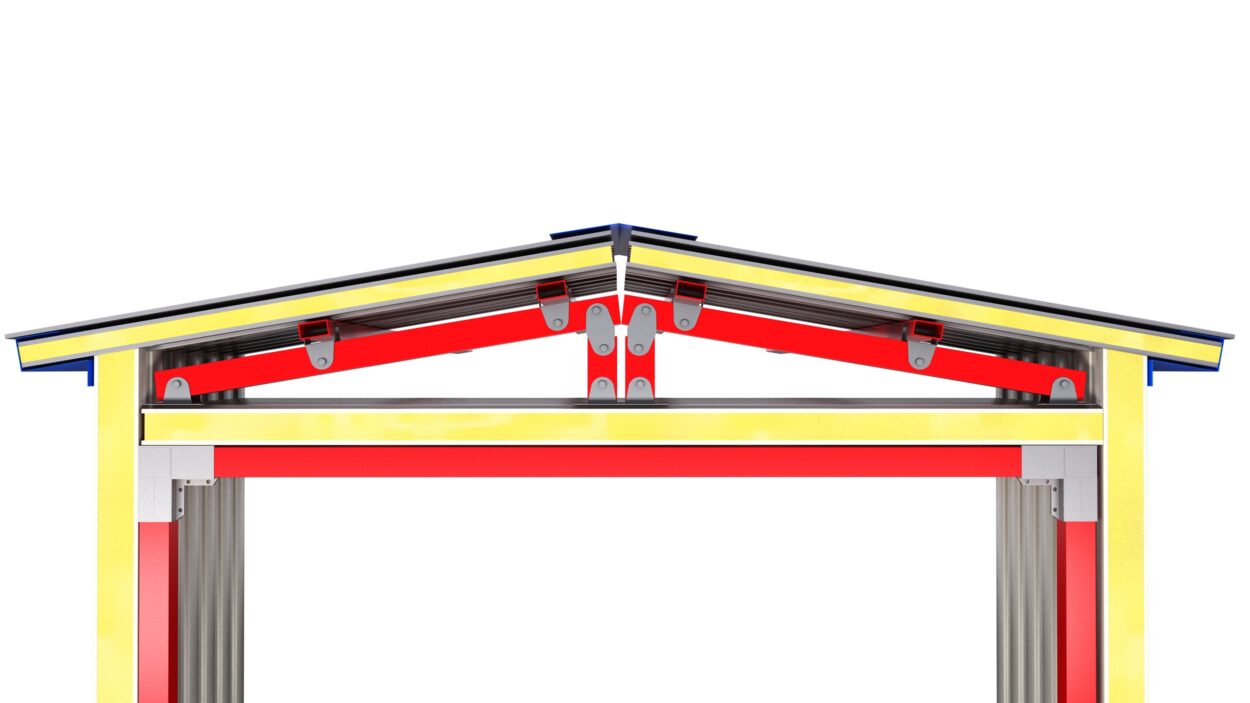
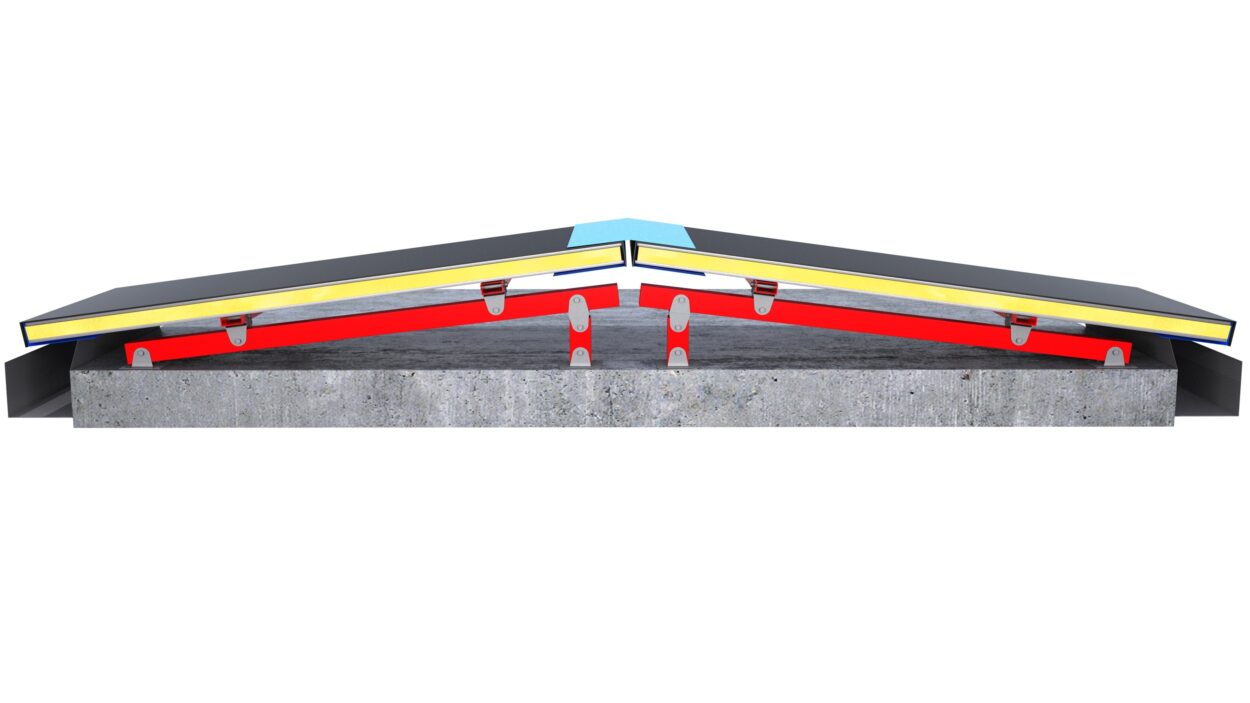
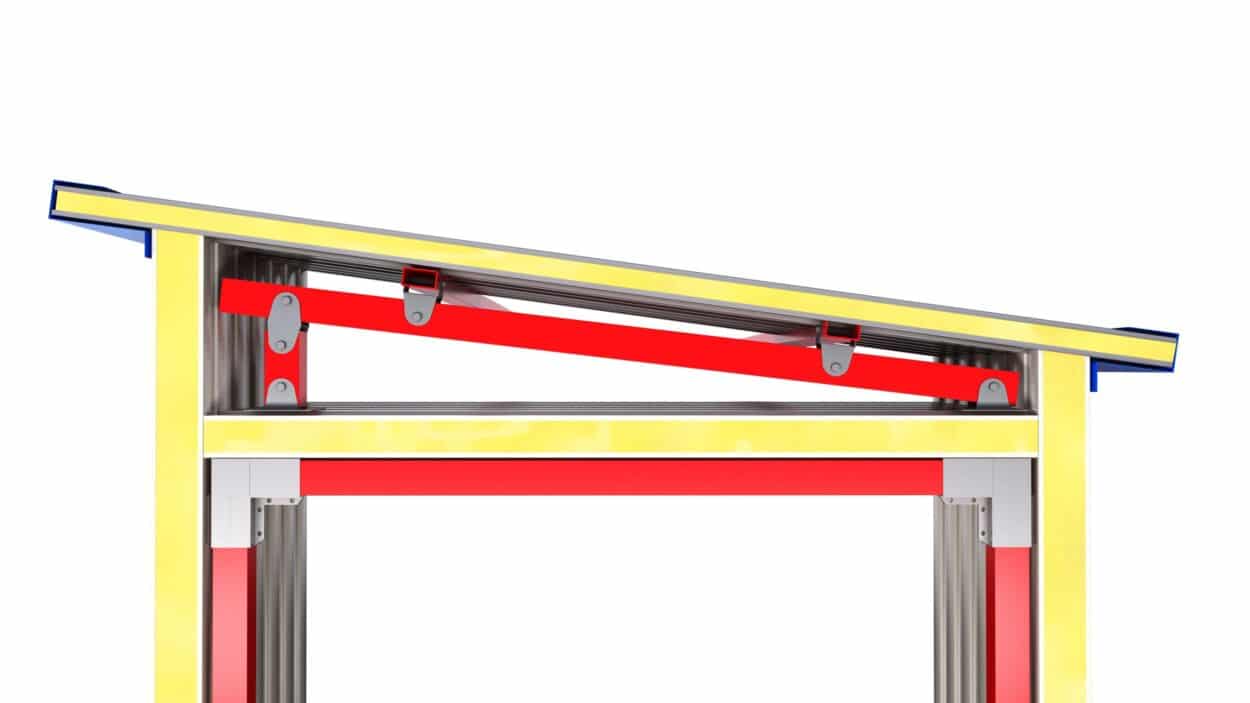
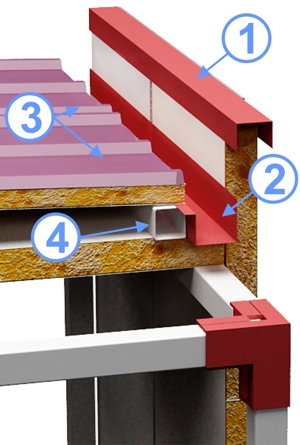
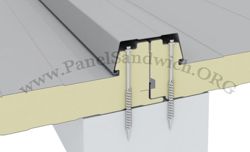
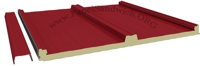
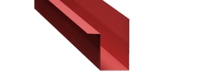
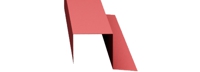
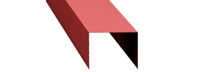
The roof is one of the fundamental elements in ensuring the strength, durability and comfort of a house. That is why we have taken the utmost care in its design and efficiency, making a functional product that improves even the highest expectations for a modern home.
In this case it is a set of elements that collaborate in the thermal and acoustic insulation of the building, being at the same time self-supporting and light, perfectly waterproofed and collaborating in the resistance of the house as a whole.
1.- Finish of 0.6 mm galvanized sheet metal.
-
- Elastic limit >= 250 N/mm².
- Base Material Quality S250GD
Breaking strength >= 330 N/mm². - Modulus of elasticity = 210,000 N/mm².
- Elongation at break min. 19%.
- Galvanized Z-275
2.- Pluvial channel of 0.6 mm galvanized sheet metal
-
- Elastic limit >= 250 N/mm².
- Base Material Quality S250GD
Breaking strength >= 330 N/mm². - Modulus of elasticity = 210,000 N/mm².
- Elongation at break min. 19%.
- Galvanized Z-275
Sandwich panels for roofs, with high mechanical strength and easy sealing, 30 mm.
-
- Inner side 0.6mm steel
- Inner side 0.45mm steel plate
- Insulation 40 kg/m3 expanded polyurethane insulation
- Type of veneer Lacquered 5 microns
- Fire Resistance CS3D0Structure tubes of 10×10 cm.
4.- Galvanized pipes of 10X10cm.
-
-
Technical specifications:
quality: s 235 (st37). -
Standards: UNE-EN 10219.
-
WALL LININGS: CEILINGS AND PARTITIONS
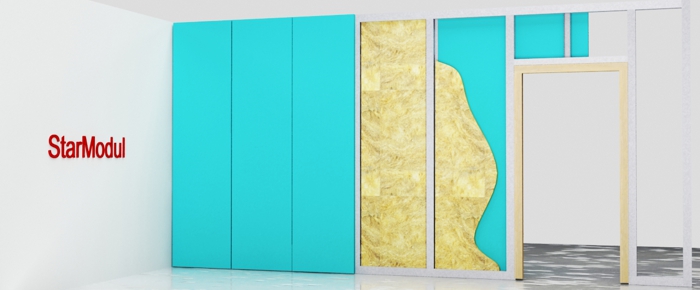

Rigid building envelope panels are based on gypsum panels (commonly called Pladur); they are light and easy to handle, they allow to create any shape, they can be applied on any surface and at any angle or inclination.
The facade linings provide structural resistance to the whole, and also provide substantial improvements in terms of insulation, by breaking thermal and acoustic bridges.
The illustration on the right shows a section of a facade wall. It is possible to appreciate how all the elements are arranged to give as a result a unique, solid set that works in solidarity with the rest of the pieces of the house.
We can observe the following pieces and elements that make up this set:
- Gypsum board (Pladur)
- Exterior façade panel
- Upper sealing channel
- Lower channel receiving Panel
- Isolation
- Plasterboard fixing omegas
- Omegas fixing uprights
With this base we can easily build the partition walls, which are called “dry” type, since no mortar (and, therefore, no water) is involved in their execution.
In the partition walls, gypsum boards are placed on both sides, reinforced and supported by a metal framework, as shown in the image on the right.
In the illustration below we see the following elements:
- Gypsum board (Pladur)
- Mounting jambs
- Upper and lower channels
- Thermo-acoustic insulation
- Door preframe
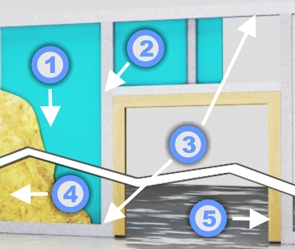
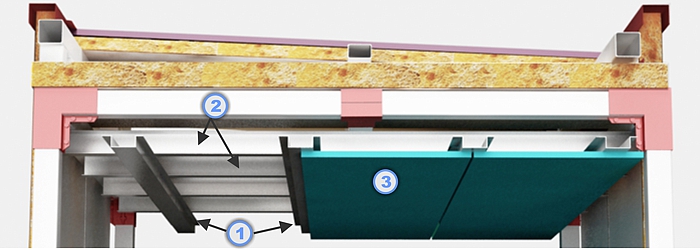
Ceiling linings also provide structural resistance to the whole, as well as substantial improvements in terms of insulation, due to the breakage of thermal and acoustic bridges.
In the illustration above we see the detail of an assembly showing the following elements:
- Omegas fixing uprights
- Plasterboard fixing omegas
- Gypsum board (Pladur)
FLOORS AND PAVEMENTS
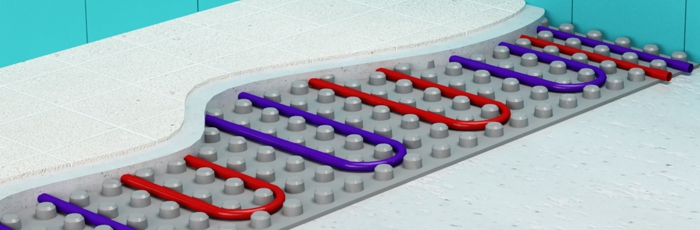
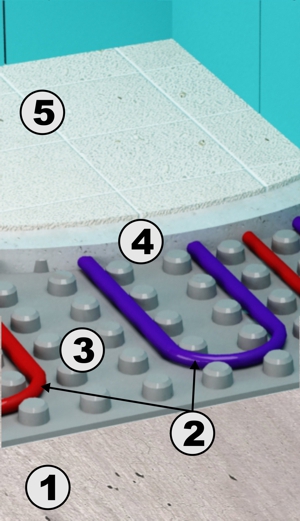
Flooring and paving make up a fundamental element in ensuring that our buildings achievethe best performance in terms of comfort and energy efficiency through thermal and acoustic insulation.
That is why we incorporate the latest technologies and market advances to achieve the highest standards.
The inclusion of underfloor heating means that the floors incorporate the following elements:
- Foundation slab
- Plastic piping with oxygen diffusion barrier. Made of polyethylene or polybutylene, especially for this heating system.
- Insulating panels on which the pipes are installed, with a moisture barrier between the subfloor and the radiant floor emitting surface placed on top.
- Cement mortar, with a recommended thickness of 5 cm measured from the upper generatrix of the pipe.
- Pavement. It can be of any type and material available in the market.
VENTILATED FACADE
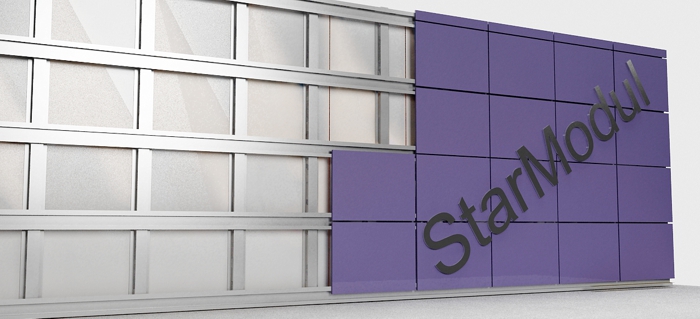
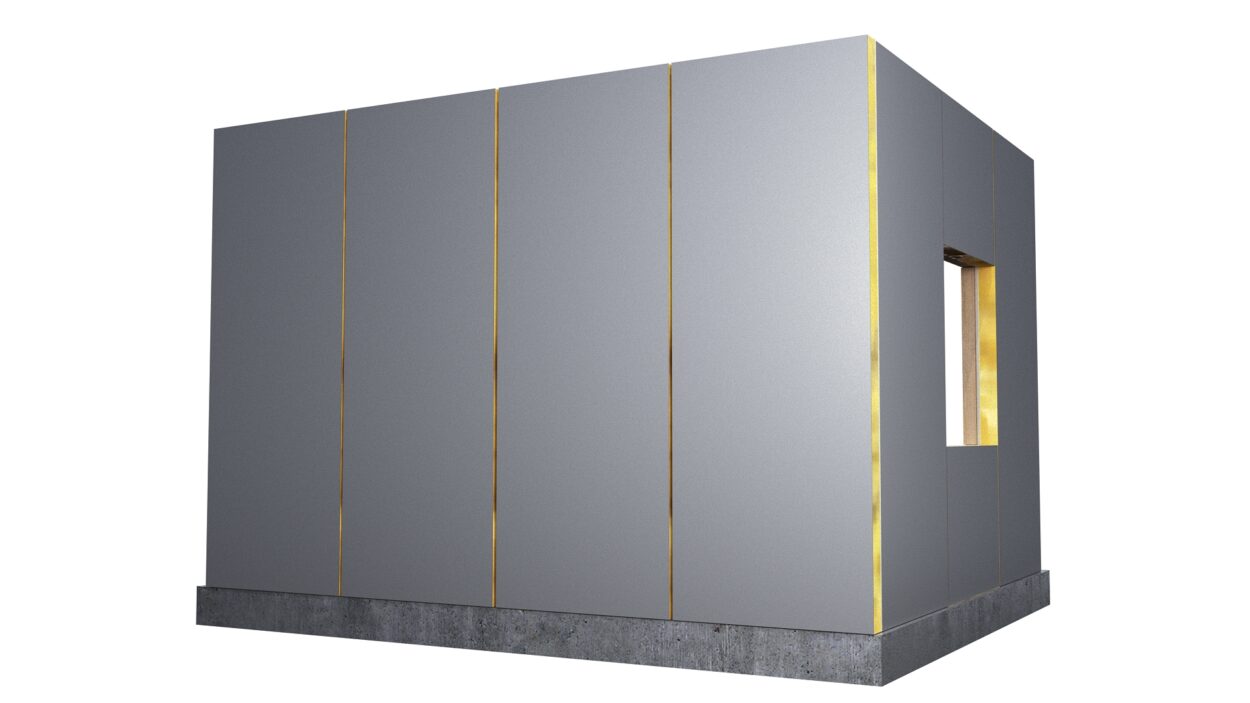
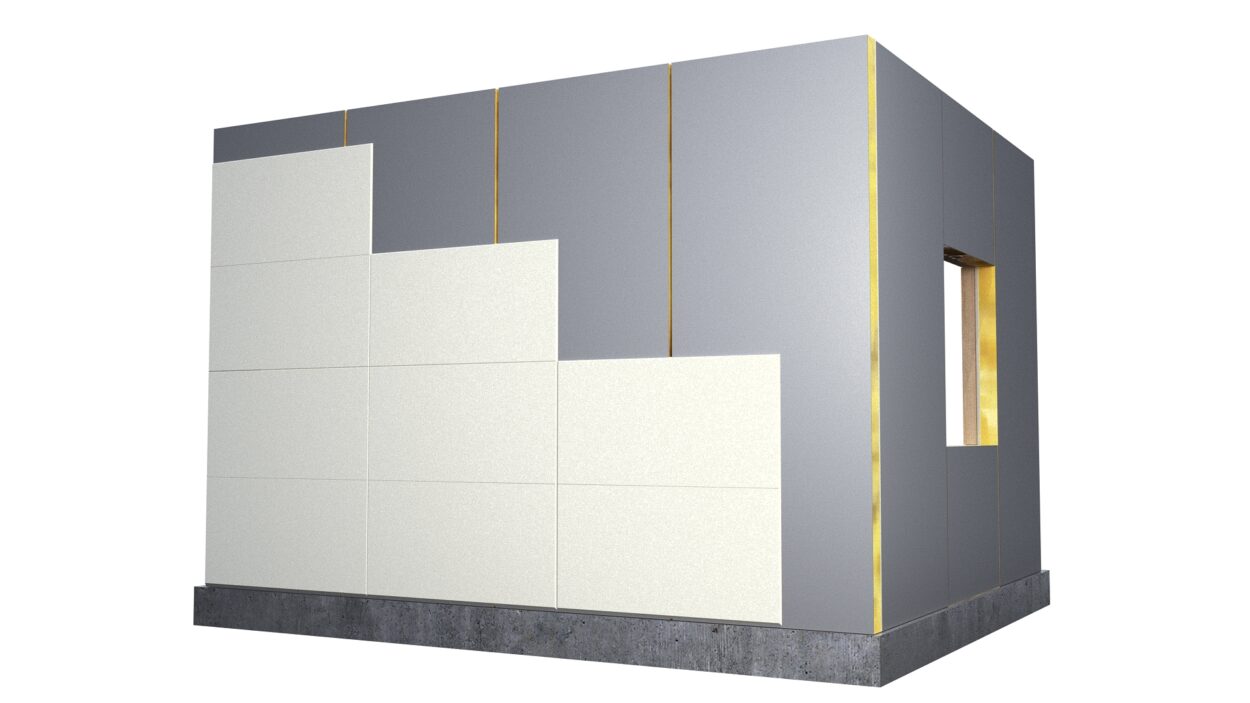
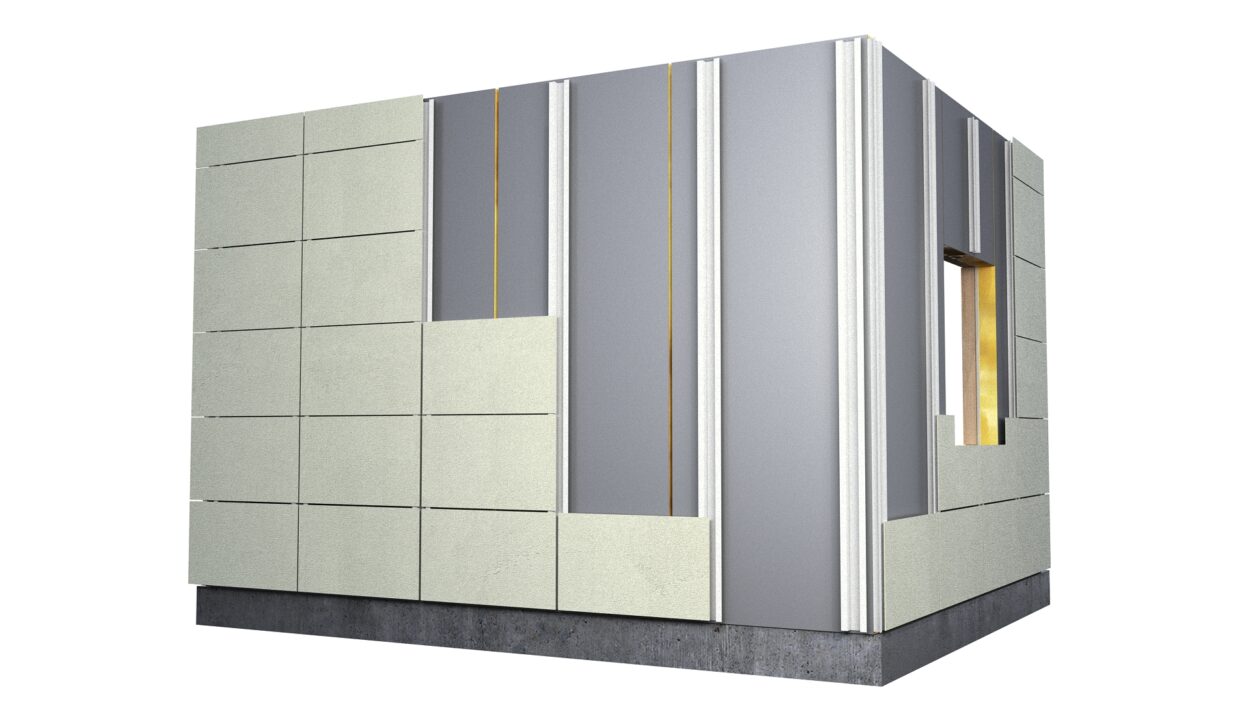
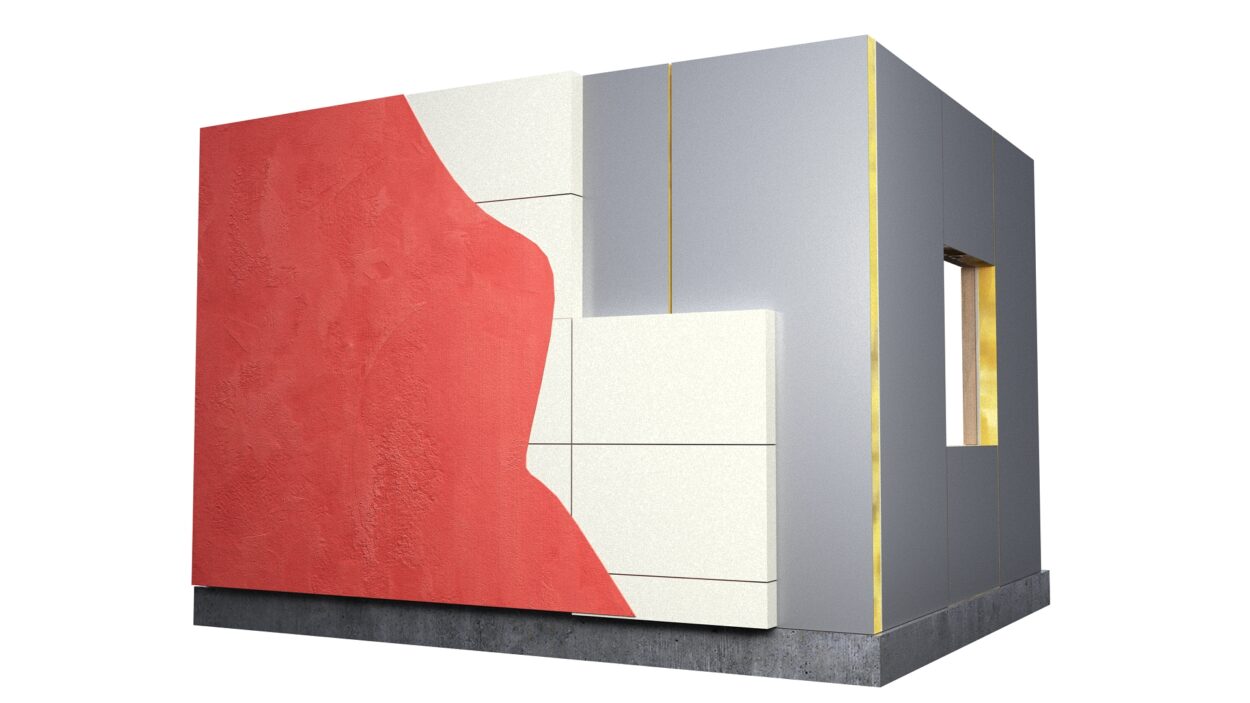
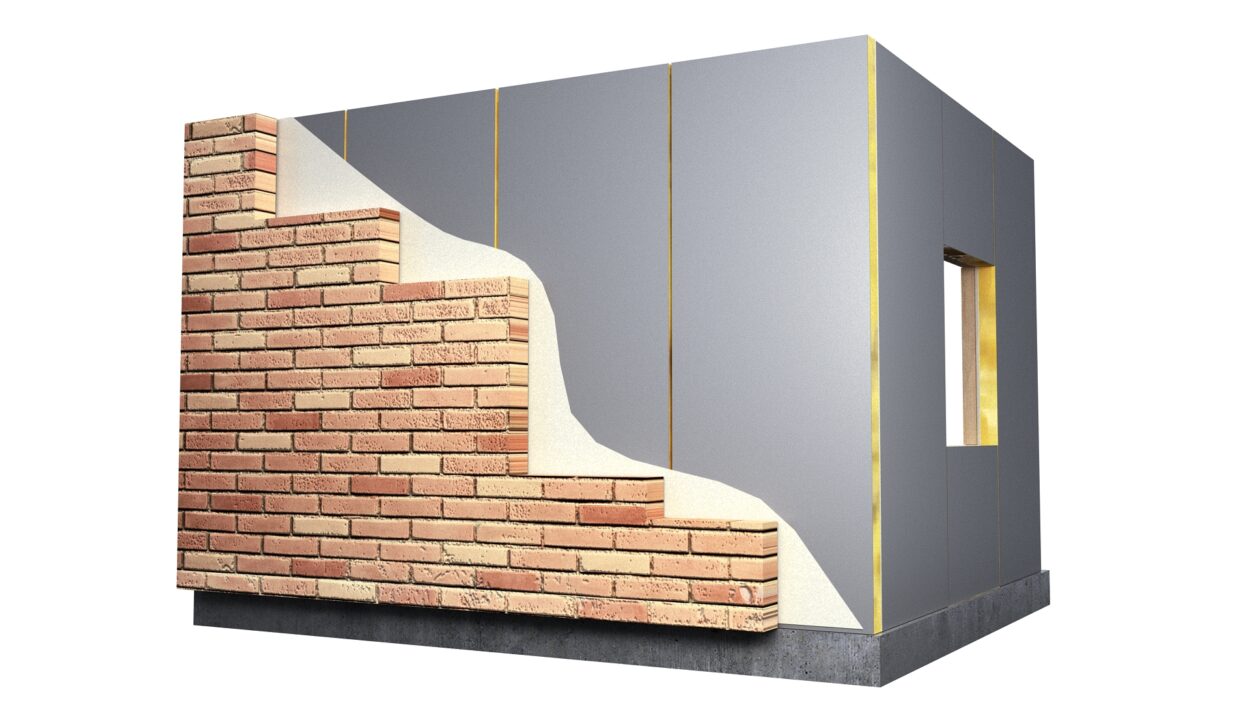
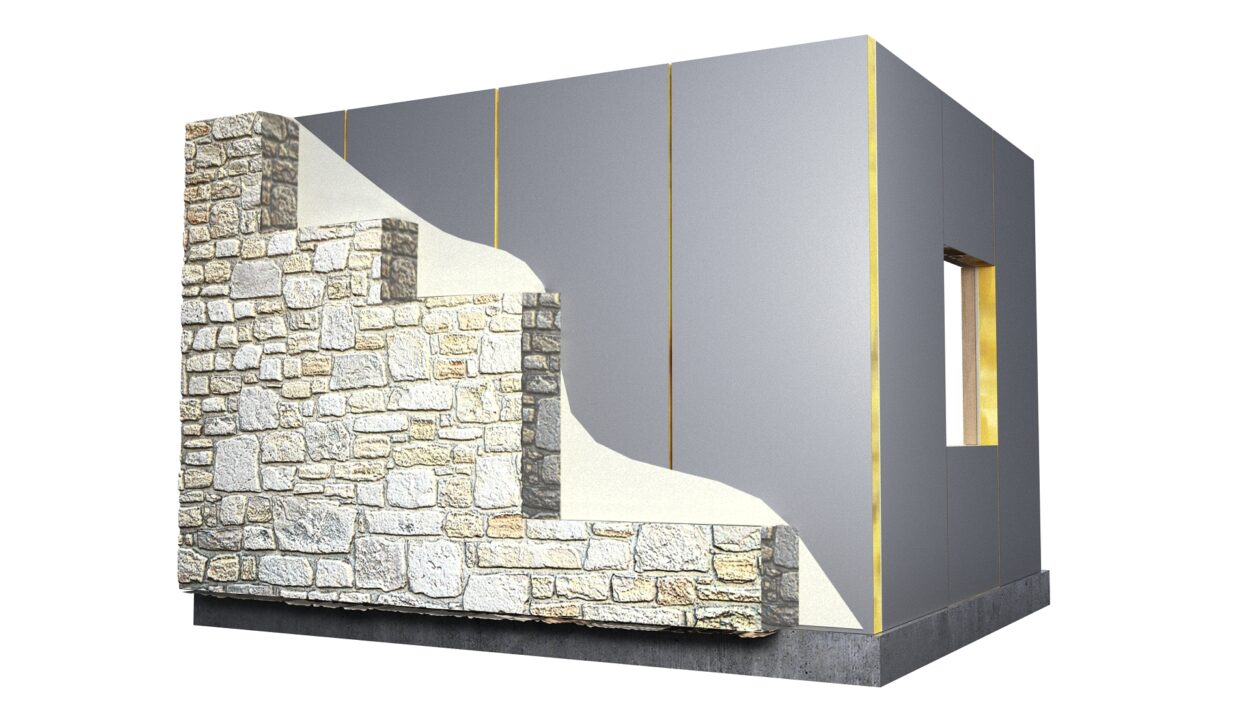
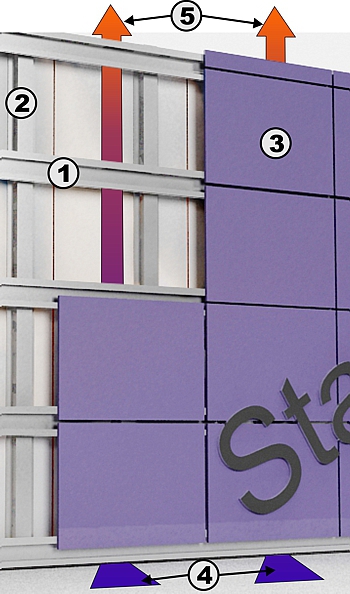
Ventilated facades are a magnificent solution to thermodynamically support the already high insulation of these buildings.
As they are separated from the facade panels, they allow constant thermal air movements, which improve insulation and prevent heat or cold accumulation.
The illustration on the right shows how a ventilated facade is assembled and how it behaves.
On the framework of the vertical (2) and horizontal (1) profiles in “Omega”, we fix the fiber cement panels (3), which keep a considerable distance between the facade panels and these.
When the sun shines on the fiber cement panels (3), they radiate heat towards the interior, causing a “chimney” effect between the façade and these panels, raising the hot air out of the framework (5) and allowing fresh air to enter from the ground (4).
It also acts in reverse, preventing cold air accumulation.
And it contributes to the acoustic insulation of the building, with a sound wave dissipation effect on the exterior panels.
- Omega” Profile
- Omega profile separator
- Painted fiber cement board
- Cold air intake
- Hot air outlet
Details of the metal structure
Examples of homes and houses with StarModul Metal Structures
In conclusion, metal structures are a great option for building houses due to their durability, strength and design flexibility. The examples set out in this article demonstrate how steel-framed houses can be not only functional, but also beautiful and modern.
With the growing popularity of metal framing kits and industrialized systems such as StarModul Steel Framing 2.0, building a home with steel has become more affordable and accessible. In addition, the metal can be recycled, making it an environmentally friendly option. Therefore, if you are thinking of building a new house, do not rule out the possibility of using metal structures: it could be the perfect solution for your needs.